Railway Bearing Cleaning Machine Plant Manufacturers & Exporters in Pune, India.
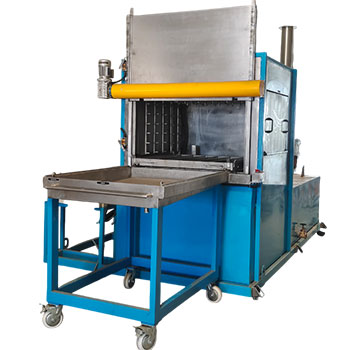
Machinery Parts
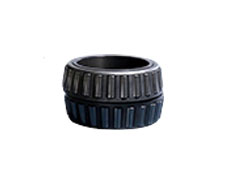
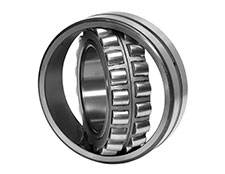
Nexon Automation is introducing Rail Roller Bearing Cleaning Plant using advanced water miscible solvent-based cleaning system. This enhanced model is specifically designed for the cleaning of rail roller bearings, for a complete degradation of grease, dust and other debris. This plant is an essential element of the periodical overhauling maintenance of rail rolling stock bearings as it guarantees their further performance and safety. cleaning techniques and methods used in this plant have environmentally friendly impacts, which makes it easy to maintain rail system and hence improving the safety and reliability of the systems, for both personnel and passengers.
Rail Bearing Cleaning Plant Technical Specifications:
Turntable Diameter | 800 to 1200 mm |
---|---|
Working Height | 900 mm |
Turntable Capacity | 400 kg to 1600 kg (Max) |
Bearing Types |
|
Individual Bearing Weight | 8 kg to 60 kg |
Maximum Diameter of Table | 1600 mm |
Construction | All wash tanks and the spray cabinet are constructed from corrosion-resistant stainless steel (SS 304) to ensure durability and longevity in harsh cleaning environments. |
Safety Features | The system is equipped with multiple safety interlocks to ensure safe operation, preventing accidental operation if doors are open or other faults are detected. |
Bearing Cleaning Plant Key Features:
- Aqueous-Based Cleaning Technology: In cleaning the roller bearings the system uses an aqueous solution making it environmentally friendly and efficient to eliminate greases, mucks, dirt among others on the rail roller bearings.
- Automatic Cleaning Cycle: All operations are fully automated so that every cleaning cycle of Cartridge Taper Roller Bearings and other roller bearing types is consistent.
- Recycling and Rinsing System: In the plant, there is a conventional washing solution recycling step and, depending on conditions, fresh water wash or recirculation of the rinse solution with rust inhibitor to protect during cleaning.
- Hot Air Blowing: Bearing cleaning is the next process, and to free them from moisture they are dried using hot air, and to set them for the next process or to reassemble them.
- Batch Type Machine with Front Loading: This is because the front-loading design is preferred because it provides convenience in loading and offloading the bearings and this reduces the amount of handling involved.
- Automated Door and Turntable System: In washing cabinet there is provision of automatic opening and closing of doors and in turntable auto slip clutch for ease in rotation along with heavy bearings.
- Solution Level Control and Heating: The tank comes with an auto-control for cleaning solution levels for correct concentrations and the water is heated using electric heaters for efficient cleaning.
- Sludge Removal System: The plant also features an automated sludge discharge mechanism that gets rid of the sludge from the washing tanks on the plant to help in prolonging the life of the washing solution and also to help in cutting the time taken to make adjustments on the plant.
Rail Roller Bearing Cleaning Machines Plant Process Flow:
- Loading: Fitted on the front-end loading turntable dependent on size and weight, the bearings can be loaded in several at a time.
- Washing: Bearings are first washed with high pressure aqueous cleaning tackle that leads to removal of dirt, grease and other contaminants.
- Rinsing: Most bearings are washed after the washing cycle and rinsed using fresh water or a rust inhibitor to minimize on the residues left behind.
- Hot Air Blowing: Bearings are then dried using a blower of hot air with a view of eliminating any moisture content that might have been trapped during the washing process so that the bearings can then be checked for suitability for research or can then be reassembled.
- Unloading: After washing or cleaning as well as drying process is over, the turntable is then unloaded to make way for bearings then the turntable bearings are ready for either service or inspection.
Additional Features :
- Rust Inhibitor Rinsing: In this step, the system has the ability of adding rust inhibitor solution in the rinsing sequence in order to prevent the bearings from rusting after washing.
- Automatic Tank Cleaning: The plant uses an automatic flowing tank that helps wash the sludge and contaminants from the cleaning solution and therefore minimizing the time that tanks will need to be cleaned.
- Corrosion-Resistant Construction: This makes it easy for plants to be corroded, and this stainless steel design ensures that they are most appropriate for long term use despite the tough cleaning solutions they are exposed to.
- Energy-Efficient Heating: The cleaning solution is then heated by means of relative cheap electric heaters to achieve the best cleaning result at the lowest possible energy cost.
Applications :
- Railway Maintenance: For the clean-up and maintenance of the rail roller bearings that are necessary in cleaning before a new process such as overhauling and in the process of making sure that they are not laden with anything that can hinder their performance.
- Automotive and Industrial Bearings: Designed for cleaning large bearings that are found in industrial and automotive applications, sealed deep groove and roller bearings included.
- Rebuild and Refurbishment Plants: Applied in outlets that renovate or reclaim bearings, in order to guarantee that these are washed properly before being reassembled or subjected to further treatment.
Why Choose Nexon’s Bearing Cleaning Plant?
- Efficient Cleaning Process: The plant offers a comprehensive cleaning regime, most especially in the areas of the bearing, in order to offer the best result.
- Durable Construction: Manufactured with the steeled sited for corrosion resistance and durable building material, the plant is meant to be durable for long time usage in industries.
- Automated Features: Through the use of an automatic door, turntable and sludge removal manual labor is minimized and the process very efficient.
- Customizable Options: The operation versatility of the system may be tailored depending on the need where aspect such as rust inhibitor selection, tank volume, and drying capabilities may be altered.