Automatic Train/Metro Wash Plant Manufacturers & Exporters in Pune, India.
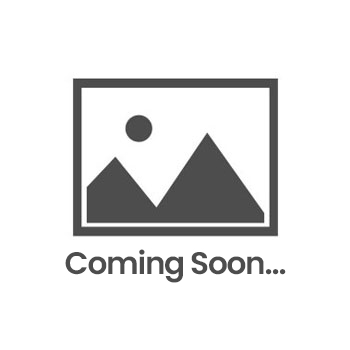
Machinery Parts
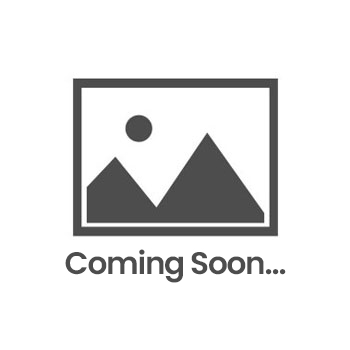
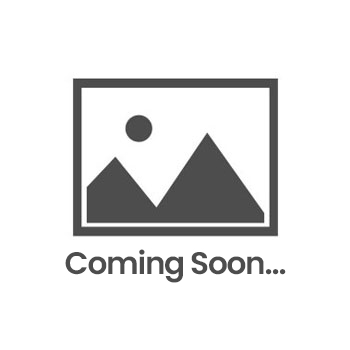
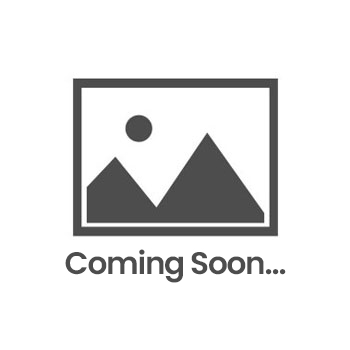
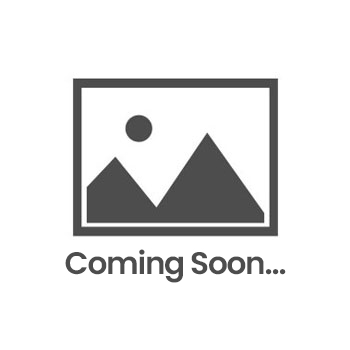
The Automatic Train Wash Plant from Nexon Automation manufacturers, suppliers & exporters in Pune, India, is built for fully automated train washing and is high capacity. It has a four-stage operating cycle whereby the plant is capable of washing the fabrics through pre-wet, detergent, brush, wash, rinse, and spin-dry. The system contains very little water, having a very efficient water recycling program; the control is complete through the use of PLC automation. They make certain that train coaches or compartments are cleaned fast and uniformly, with limited human interference, making certain that the processes of rail networks’ maintenance are enhanced.
Automatic Train/Metro Wash Plant Technical Specifications:
Washing Process | Automatic and Manual Modes |
---|---|
Flow Rates |
|
Brushes | Vertical and horizontal brushes with water spray integration |
Air Blowers | 4.5 cubic meters at 0.8 bars for water streak removal |
Control Systems | Fully automated PLC control with local and depot control options |
Train Washing Plant Key Features:
- Fully Automated Operation: The plant has automatic as well as the manual mode of operation with automatic turn on and off through sensors whenever the train is approaching the wash plant or leaving the plant.
- Pre-Wetting and Detergent Spraying: Recycled water is used to wet surfaces of trains before washing and thereafter uses detergent spray to facilitate washing of trains.
- Vertical Brushes: There are two pairs of vertical brushes on both sides of the train that scrub the body and windows mechanically wiping them off stains and dirt.
- Brushing Stages: The brushing is done in two phases, the first by using effluent water and then the phantase water to avoid mixing the two types of water.
- Final Rinse with RO Water: Use of regent quality RO water is used in the last wash to minimize formation of ‘water streaks’ on the garments.
- Water Recycling Module: All used water so produced undergoes a water recycling treatment in order to optimise the utilisation of water by the centre with minimum wastage.
- Air Blower Drying: After the wash high-capacity air blowers are used to blow off the water thereby eliminating water streaks and making sure that the exterior of the train is dry.
Process Flow:
- Pre-Wetting: When the train gets inside the plant, water is again splashed on both sides of the train to cool the train before it is washed by detergent.
- Detergent Station: Special detergent is sprayed through the outlets and wash the train, using a solution with a right PH level so as not to decayed the paints and other outer parts of the train.
- Brushing: Whilst some circular brushes clean the sides of the train, water is at the same time splashed onto the train for cleaning purposes.
- Rinsing: Once again, it is also done in two stages; first with softened water and the second stage being the reverse osmosis water simply to get the car sparkling clean.
- Air Blow Drying: Other equipment includes moisture blowers which strip the train of moisture preventing streaks and ensuring the train dries up quickly.
Additional Features:
- Reverse Osmosis Plant (RO): Guarantees availability of clean water at the last wash in order to ensure there is no streaking and that it leaves a quality finish.
- Water Recycling Module: Recycles water from pre-wetting, detergent spraying and brushing stage, so that it reduces the consumption of fresh water.
- Advanced Safety Features: The plant also uses sensors and limit switches to track train movement and washing related operations. Any disturbance such as incorrect speed in the train or incorrect RPM of the brush will stop the plant.
- Illuminated Signage: The track has several signs along it that indicate the Train drives on the plant and the recommended speed to maneuver.
- Remote Monitoring: The system also incorporates a remote monitoring system for recording operational information, cycle frequency, and water consumption for the purpose of reviewing system performance.
Applications:
- Railways and Metro Systems: Perfect for mid and long-haul rail, daily and metro commute, providing thorough cleaning efficiently without train being off the tracks often.
- Public Transport Systems: Applied in depot depots to ensure a number of trains are cleaned within a short period.
- Industrial Rail Networks: Recommended for the cleaning of reusable industrial rail vehicles which may need frequent washing.
Why Nexon’s Automatic Train Wash Plant?
- Efficient Water Usage: Due to the integrated water recycling system, fresh water use is dramatically minimized making the system sustainable to the environment and cheaper.
- High Productivity: Subsequently, the design and technology used allows Tricon to wash trains in continuous production line fashion with little interference in order to maintain high levels of throughput.
- Customizable Settings: The operational parameters of the washing cycle include parameters like water pressure, or brush speed, and the composition of detergent can be optimized to given specifications.
- Durable Construction: Sited and constructed from proven, corrosion friendly materials, the plant is built to withstand the extreme challenges of the delivery environment.